Success Story: How Avastro Inc. Transformed a Client's Fulfilment Operations
Introduction
In the fast-paced world of logistics and supply chain management, efficiency and reliability are key. Avastro Inc., a leading supply chain solutions provider, recently helped a client revolutionize their fulfillment operations, achieving remarkable results in a short period. This success story highlights the strategies employed and the outcomes achieved.
The client, a mid-sized e-commerce business, faced significant challenges in their order fulfillment process. Delays and inaccuracies were affecting customer satisfaction and impacting their bottom line. Recognizing the need for transformation, they turned to Avastro Inc. for support.
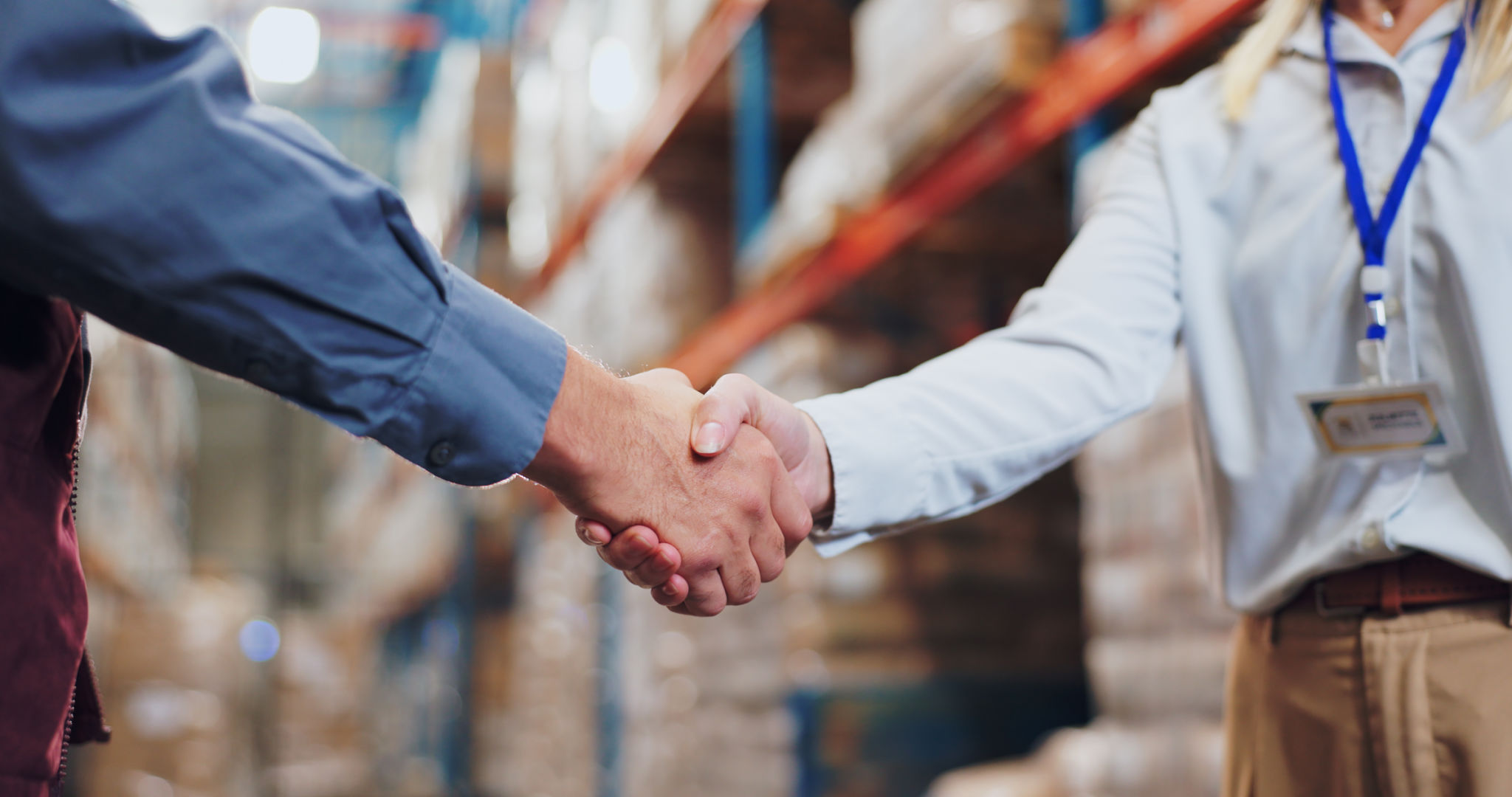
Understanding the Challenges
Before devising a solution, Avastro Inc. conducted a thorough analysis of the client's existing operations. The team identified several critical issues:
- Inefficient warehouse layout leading to delayed order picking.
- Lack of real-time inventory tracking causing stock discrepancies.
- Manual processes increasing error rates and slowing down operations.
These challenges were not uncommon in the industry but required strategic interventions to overcome. Avastro Inc. initiated a comprehensive plan to address these issues systematically.
Implementing Innovative Solutions
The first step in transforming the client's fulfillment operations was redesigning the warehouse layout. Avastro Inc. applied advanced data analytics to optimize space utilization, reducing travel time for pickers and streamlining the workflow.

Next, an automated inventory management system was introduced. This system provided real-time visibility into stock levels and locations, significantly reducing discrepancies and ensuring accurate order fulfillment. By integrating this technology, the client was able to maintain optimal inventory levels and improve their reorder process.
Automating Processes for Efficiency
To address the manual processes that were slowing down operations, Avastro Inc. implemented automation solutions. These included automated conveyors and sorting systems that expedited order processing while minimizing human error. As a result, the client saw a substantial improvement in processing speed and accuracy.
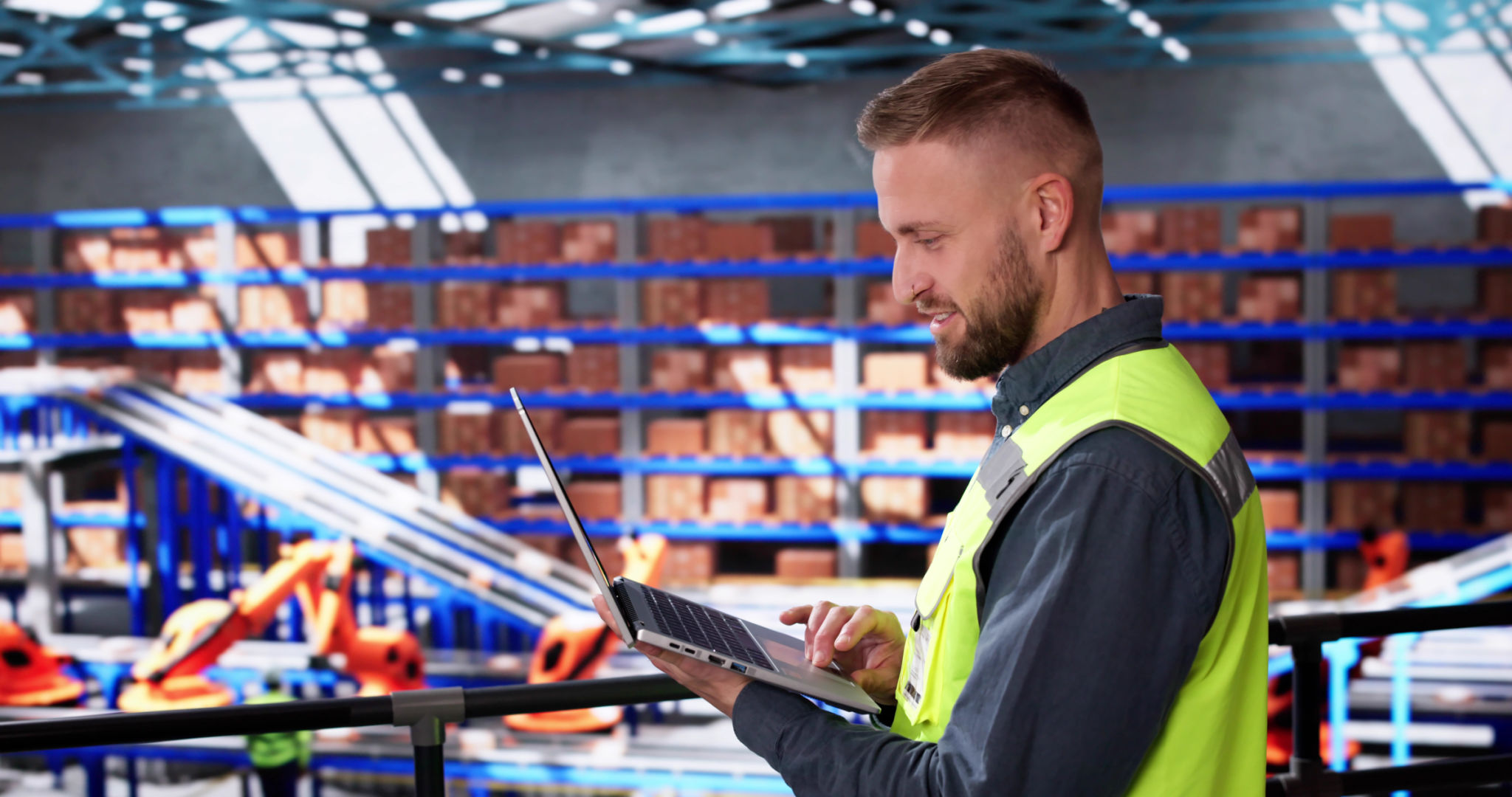
Results and Impact
The impact of these changes was immediate and significant. Within months, the client's fulfillment operations saw:
- A 40% reduction in order processing time.
- An increase in order accuracy to 99%.
- A noticeable improvement in customer satisfaction scores.
Moreover, these enhancements led to cost savings through reduced labor expenses and minimized returns due to errors. The client's overall operational efficiency improved, allowing them to scale their business with confidence.
Conclusion
The transformation of the client's fulfillment operations by Avastro Inc. is a testament to the power of strategic planning and innovative solutions in supply chain management. By addressing key challenges with targeted interventions, Avastro Inc. enabled their client to achieve operational excellence and meet the demands of an ever-evolving market.
This success story serves as an inspiration for other businesses facing similar challenges, demonstrating that with the right partner, overcoming operational hurdles is not only possible but can lead to significant growth and success.